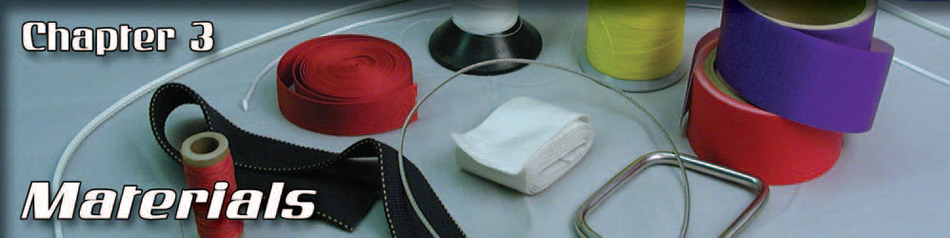
The correct identification and use of the various materials
in parachute manufacturing and repair are of vital
importance to all riggers. Just as important as acquiring
knowledge of tools and machines, the language of materials
is a necessary part of a rigger’s job comprehension. In
doing repairs or alterations, the rigger must be able to
identify the types of materials used in order to duplicate
the original manufacture or ensure the correct level of
safety necessary. Some materials may look similar, but
there can be subtle differences between them that make a
major difference in their strength or durability.
It is not the intent of this chapter to present information
on every type of material or hardware ever used in parachutes.
For those materials used in obsolete or military
surplus parachutes, there are reference sources, such as
The Parachute Manual by Poynter, for the rigger to use to
identify older materials. The intent of this chapter is to
present as much information as possible on the modern
materials used in today’s parachute systems.
Most riggers operate quite successfully at a basic level of
material knowledge. There are certain materials that are
in common use on most parachute systems, and in dealing
with these on a regular basis, the rigger becomes very
familiar with their use and characteristics. It is necessary
that the rigger know their correct type, nomenclature,
strength, and common use. In dealing with other riggers,
manufacturers, and suppliers, the rigger is then able to
identify the referenced material in order to obtain the
appropriate repair part or describe the use of the material
to others. All of this is part of the parachute “language”
required for the rigger to operate under.
SPECIFICATIONS
All certificated parachute systems built under
Government approval programs require most, if not all,
materials used in their construction to have some form of
specification approval. The most common of these systems
is the military specification (MIL-SPEC) system.
In addition, there are other Government specifications,
such as Federal Standards, and commercial specifications
in use. The MIL-SPEC system is the one with which most
riggers are familiar. Contrary to popular perception, not
all materials for use in parachute manufacturing must be
MIL-SPEC. Any specification may be used, providing the
manufacturer can prove compliance with this specification,
and that the specification is acceptable to the FAA
for use in the parachute system. As a rule, the MIL-SPEC system has proven the most readily available and
accepted method.
In recent years, the Government has been accepting more
commercial specifications in lieu of MIL-SPEC items. In
2002, the Parachute Industry Association (PIA) adopted
approximately 270 parachute related specifications,
drawings, standards, and test methods. The PIA takes
responsibility for the continued maintenance and revision
of these specifications. As the specifications are revised,
they keep their original identification number, but the PIA
prefix precedes them. For instance, MIL-W-4088 webbing
becomes PIA-W-4088. Through the involvement of
the PIA Specifications Committee, the revised specifications,
including new digital drawings, are made available
to the industry.
The MIL-SPEC or PIA-SPEC system of identification
consists of the initial letters MIL or PIA with a middle
letter such as W for webbing or wire, then the identification
or serial number of the specification. In addition,
there may be a revision letter such as A, B, C, D, etc. In
the case of PIA-W-4088D, this is the fourth revision.
The materials and hardware listed herein are only a small
part of those available but the most commonly used in the
majority of today’s rigging profession. By learning the
specifications and uses of these materials, the rigger
establishes a sound basis for the repair and maintenance
of modern parachutes.
To promote the latest specifications, the PIA nomenclature
is called out unless otherwise noted. In the past, the common
method to denote the various types of webbings,
cords, etc., was to use the Roman numeral for the type (i.e.,
Type VIII for Ty-8, Type XVII for Ty-17, etc.). For this
book, the standard is the Arabic numeral (i.e., Ty-7, etc.).
Many of the figures in this chapter use a neutral background
with an XY grid for reference. The numbers are
one-inch increments for a proportional reference.
FABRICS
Fabrics for use in the manufacturing of parachutes are
predominately nylon. The major differences include the
weave, weight, and finish. The various types of materials
include canopy fabric, pack cloths, mesh, elastic fabrics,
stiffener materials, and foams.
Canopy fabrics are primarily ripstop nylon. Ripstop
weave is a plain weave with heavier threads woven into
the material resulting in a boxlike pattern. The heavier
thread inhibits the tearing process and results in stronger
fabrics. [Figures 3-1 through 3-6]
The composition of most containers is from either nylon
duck (para-pak) for military systems or Cordura® for
sport systems. Most sport containers also utilize a thin
foam lining on the inside of the flaps to smooth out the
fabric and absorb wear and tear. Other fabrics, such as
mesh, Spandex®, and ballistic fabric, serve specialized
purposes. [Figures 3-7 through 3-15]
|