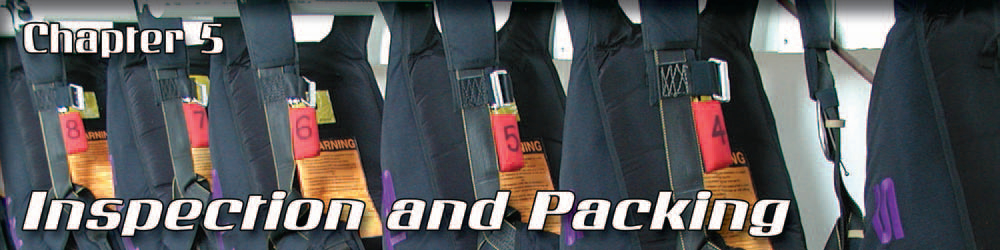
For most people, parachute rigging is all about packing
parachutes. Rigging and packing may be synonymous,
but there is a distinct difference. In its truest form, parachute
rigging is the practice of assembling a parachute
system with its various components into an operative
assembly. Packing is the practice of folding the parachute
canopy in an organized manner such that it fits into the
container system and allows the canopy to open when the
user activates the system.
There are five distinct stages involved in packing the
parachute. They are:
1. Identification.
2. Inspection.
3. Rigging and/or repairs.
4. Packing.
5. Documentation.
IDENTIFICATION
The first thing the rigger should do when a customer
brings a parachute in for packing or repair is to confirm
that the owner’s information is correct on the packing data
card. This ensures that the rigger’s logbook entry is accurate.
In a commercial loft, a work order is filled out with
all the correct information about the customer and the
parachute. Many modern lofts input this information into
a computer database for tracking their customers. This
data is then used to send automatic repack notices to customers.
This ensures that the reserve or emergency parachute
is legal to use when the customer needs it.
INSPECTION
The owner should bring the parachute to the rigger in
its packed condition. This practice should be encouraged
for several reasons. The canopy is a fragile item
and is subject to damage or contamination if left
exposed to the elements, and the container is designed
to protect the canopy from damage. The parachute
should be opened only in the controlled environment
of the parachute loft. This is so the entire system can
be examined externally for signs of damage or contamination
before it is opened. Next, the owner needs to don the parachute and pull the ripcord as in a real life
scenario to understand the correct fitting of the harness
and how to activate the system properly. This gives the
owner a great degree of confidence that the parachute
will work when needed. Doing so also lets the owner
know that the parachute will indeed be repacked and
not just “pencil packed.”
Generally, customers leave the parachute to be repacked;
however, riggers should encourage their customers to stay
and observe the repack. Many riggers encourage this
behavior since it results in a more educated individual. In
a busy loft environment, however, a scheduled appointment
might be needed to allow for the increased time necessary
to explain the process. If the customer decides to
watch the repacking, the rigger should allow at least twice
the usual time for the project. This allows the customer to
ask questions, which results in a more educated and safer
parachute user. Another benefit of this is that the customer
gets to see the effort it takes to service a parachute.
Figure 5-1 on page 5-2 shows a packing flow chart that
details the sequence of events the rigger should follow
from receiving the parachute to collecting the money
from the customer.
Upon completion of the visual inspection, there are two
options for continuing. If there are no visual indications
of damage or contamination, move on to the next step of
opening the parachute. If something suspicious is found,
or if there is a hole in the container or discoloration to the
container fabric, the rigger needs to see if the damage
penetrated into the canopy. To do so, note the location and
check internally after opening the parachute.
If owners are participating in the inspection, it is a good
idea to have them backed against the packing table or similar
surface when they pull the ripcord so the canopy will
not fall out on the floor. This keeps the canopy clean, but
it also lets the rigger control the extraction of the canopy
from the container. It is good practice to hold the canopy
in the container while the owner takes off the pack.
Placing the rig on the table allows the rigger to thor- oughly examine the previous pack job and to check
those areas previously identified as damaged or contaminated.
During the examination of the parachute for damage or
contamination, the rigger should also look at how the
previous rigger packed the canopy. Particularly in
regard to pilot emergency parachutes, riggers sometimes
exercise great latitude in interpreting the packing
instructions in order to make the parachute as comfortable
as possible for the pilot. Each rigger makes the
determination as to what is the correct packing method.
If the present rigger finds that the last pack job was in
error, the individual responsible needs to be notified of
the findings.
The rigger next should verify the make, model, and
serial number of the parachute. Sometimes the canopy
may have been changed in an assembly, particularly in
a sport rig. For sport rigs and some emergency rigs, be sure to check the Automatic Activation Device (AAD).
The newest data cards provide space for information
on the AAD to include service cycle and date of last
battery replacement. With the recent widespread
acceptance of AADs, this is one area the rigger cannot
overlook.
The battery life cycle and the unit service life cycle,
and how they interface with the repack cycle of the
parachute, are very important things to consider. The
major question the rigger must ask is: If the battery or
unit service life expires during the upcoming repack
cycle, should the rigger pack the parachute and seal it,
thereby certifying it for the next 120-day repack cycle?
A comparable situation would be if an airframe and
powerplant mechanic signs off an annual inspection
on an aircraft. The mechanic is saying that the aircraft
is airworthy at that time. However, the mechanic is not
responsible for the future status of the aircraft if the
emergency locator transmitter (ELT) is due for battery service during the next year that the annual is valid.
That responsibility lies with the aircraft owner. This
scenario can be reasonably extended to the AAD and
parachute. Generally, however, most riggers refuse to
pack the parachute if the battery or unit life cycle
expires during the 120-day repack cycle.
Some AAD manufacturers have specific rules regarding
battery and repack expiration dates. For example,
the manufacturer might mandate that if the battery life
expires during the 120-day repack cycle, then the rigger
is not to pack it unless the batteries are replaced or
the unit is removed from the assembly. Regarding the
4-year service cycle, there is a 90-day grace period for
servicing. If the 120-day repack cycle expires within
that 90-day period, then the rigger may repack and recertify
the assembly. If the repack cycle extends past
the 90-day period, then the rigger should not pack the
assembly with the AAD. In any case, the rigger should
follow the directions of the AAD manufacturer for that
particular make and model of AAD.
The rigger must make sure to have the latest revision
of the packing instructions as well as any pertinent
service bulletins from the manufacturer or
Airworthiness Directives (AD) issued by the FAA. The
rigger may have a set of packing instructions that specifies
a certain method for folding the canopy. However,
the manufacturer may have changed the method and
issued a revision to the manual or a complete new one.
If the rigger is not completely sure that he/she has the
latest information, then it’s time to use the most valuable
tool in their inventory—the telephone. A quick
call to the manufacturer is all it takes to get the latest
information. Most manufacturers publish their service
bulletins in hard copy format and on their Web site. In
addition, the Parachute Industry Association (PIA) also
has a listing of service bulletins at www.pia.com. It is
most important that all riggers make an effort to maintain
a comprehensive library of packing instructions
and their associated service bulletins. Under Title 14 of
the Code of Federal Regulations (14 CFR) part 65, subsection
65.129(e), the certificated rigger may not
“pack, maintain, or alter a parachute in any manner that
deviates from procedures approved by the
Administrator or the manufacturer of the parachute.”
In addition, 14 CFR, subsection 65.129(f) also states
that the certificated rigger may not “exercise the privileges
of his certificate and type rating unless he understands
the current manufacturer’s instructions for the
operation involved.”
|