Chapter 5
COMPONENT COMPATIBILITY
Once the rigger has all of the current manuals and information,
the inspection can continue. This covers not just
the canopy but also the entire assembly. In addition to
looking for damage or contamination to the system, the
rigger must make sure that all of the component parts are
compatible and approved by the manufacturer. Figure 5-2 shows a sample parts list for a typical sport parachute,
having dual parachutes in a single harness system (a piggyback).
This parts list delineates exactly what parts are
used in the assembly of the system. The rigger should
check each component part and its identifying label or
stamp against the parts list. Mismatched component parts
are among the most frequent problems found in the field.
Many riggers are under the impression they can freely
interchange component parts, but this may be done only
within certain limits. Paragraph 11(a) of Advisory
Circular (AC) 105-2C, Sport Parachute Jumping, states:
“The assembly or mating of approved parachute components
from different manufacturers may be made by a certificated
and appropriately rated parachute rigger or
parachute loft in accordance with the parachute manufacturer’s
instructions and without further authorization by
the manufacturer or the FAA. Specifically, when various
parachute components are interchanged, the parachute
rigger should follow the canopy manufacturer’s instructions
as well as the parachute container manufacturer’s
instructions. However, the container manufacturer’s
instructions take precedence when there is a conflict
between the two.” In figure 5-2, note the bold print at the
bottom of the page: “NO SUBSTITUTION OF COMPONENT
PARTS IS AUTHORIZED!” This manufacturer
specifically states that you cannot use anything other than
Original Equipment Manufacturer (OEM) parts.
Substituting other parts places the rigger in violation of
the Code of Federal Regulations.
A common problem found in the field concerns reserve
ripcords. Several manufacturers of sport rigs use a onepin
ripcord with a mini trapezoidal handle and a cable
length 27-29 inches long. Depending on the actual container
it goes into, it’s possible to use one manufacturer’s
ripcord in another container as long as the rigger feels
there is sufficient excess cable for safety reasons.
However, imagine one ripcord is 27 inches overall and is
used in a system that is approved under Technical
Standard Order (TSO) C-23b and is rated at 300 pounds.
Another ripcord is 28 inches overall and is used in a
system approved under TSO C-23c, and is rated at 600
pounds for use with a Reserve Static Line (RSL) installation.
The problem here is the mating of different TSO
standard components. Installing the first ripcord in the
second container with an RSL lanyard may be degrading
the safety aspect of the system. So how does the rigger
tell which is which? The ripcord approved under
TSO C-23b will have minimal markings, perhaps only a
manufacturer’s part number. The ripcord approved
under TSO C-23c will have several markings on the handle
as required by the TSO. It should have the manufacturer’s
part number, manufacturer’s identification,
TSO-C23c, and the batch or serial number or date of
manufacture. [Figure 5-3] In reality, as long as the cable
lengths are compatible, the function of the ripcord will
probably work. The problem surfaces in the event of a
problem or incident involving the system. At this point,
the FAA could find the mismatched component and take
action against the rigger who packed the parachute.
A bigger problem surfaces when the rigger substitutes a
reserve deployment bag made by another manufacturer.
Most reserve deployment bags are compatible with the
appropriate container based on dimensions and volume.
If the deployment bag does not fit correctly, there can be
a problem with proper functioning of the system. These
are two examples of the more common compatibility
issues that are regularly found in the field. There are others
that the rigger may encounter and need to address as
well. The best solution is for the rigger to follow the manufacturer’s
parts list strictly to ensure the safety of the
parachute system.
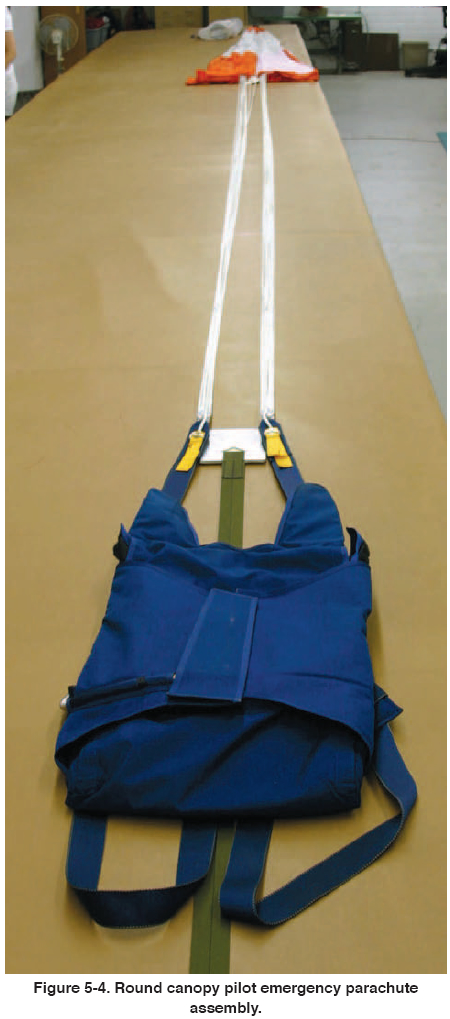
After the rigger has determined that all of the component
parts are compatible, he/she can now commence the
actual inspection of the parachute assembly. Figure 5-4
shows a typical pilot emergency parachute assembly with
a round canopy laid out on the packing table. Make sure
the canopy is straight and the apex lines are even. Then
apply firm tension to the canopy and lines using a tension
board. The standard is to start at the top of the assembly.
This assembly in figure 5-4 can be broken down into six
separate areas. They are:
1. Pilot chute and bridle.
2. Canopy and deployment device.
3. Suspension lines and connector links.
4. Container.
5. Harness including risers.
6. Ripcord.
Inspection/packing checklists allow riggers to track their
progress as they do their inspection. [Figure 5-5] It is
desirable for riggers to complete their inspection uninterrupted,
which ensures that the inspection process is
followed and nothing gets overlooked. This rarely happens,
however, due to normal interruptions such as phone
calls or customer questions. Using the inspection checklist
ensures that after an interruption, the rigger is able to continue at the proper spot without missing anything.
This checklist is divided into seven sections that make it
usable for all types of parachute assemblies. It includes
an area for counting the tools at the beginning and end of
the inspection and packing procedure. This ensures that
no tools are overlooked or left in the parachute. While this
may sound implausible to some, it has happened over the
years, sometimes with fatal consequences.
|