October 13, 2014 - Over the last several weeks,
crews at GE Aviation’s flight test base in
Victorville, CA,
at the edge of the Mojave
Desert, installed a next-generation
jet engine with ceramic components and 3-D
printed parts to the wing of a modified Boeing
747, and readied it for its maiden flight. The
engine, called LEAP, successfully took to the
skies last Monday.
The LEAP engine was developed by CFM
International, a joint venture between GE and
France’s Snecma (Safran). The engine’s unique
design and materials make it 15 percent more
fuel efficient than comparable CFM engines
already powering thousands of Boeing and Airbus
planes. It is also lighter, quieter and produces
fewer emissions. CFM estimates that the LEAP can
save an airline as much as $1.6 million in fuel
costs per plane per year.
There are three versions of the jet engine: the
LEAP-1A for the new Airbus 320neo passenger
jets, the LEAP-1B for Boeing’s 737MAX aircraft,
and the LEAP-1C for China’s
COMAC C919 planes.
|
|
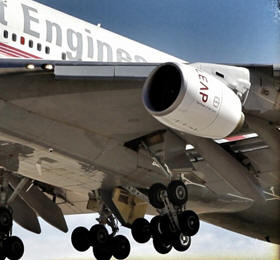 |